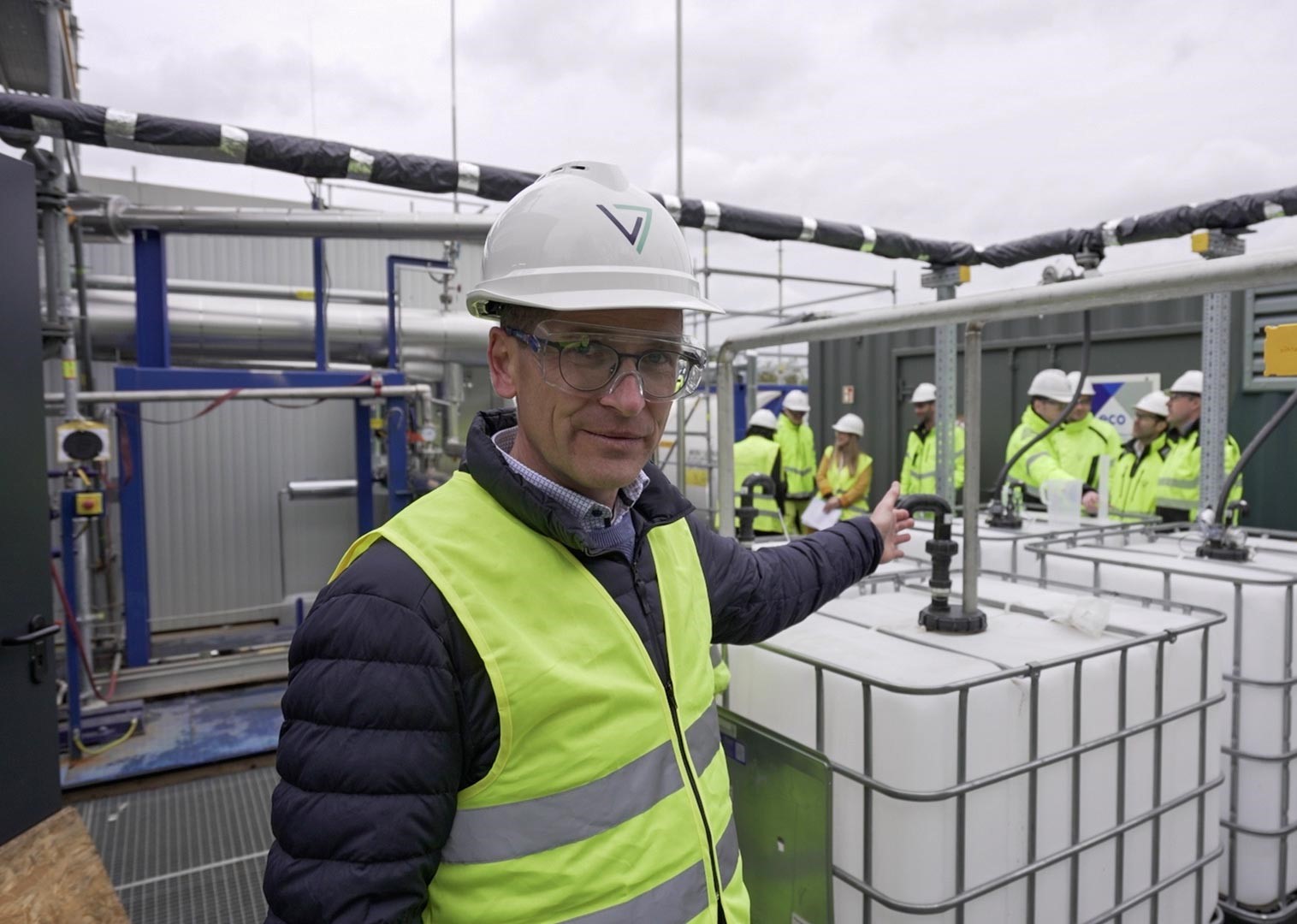
First Lithium Chloride produced from Optimisation Plant
Start of production of lithium chloride from a local resource in Europe Important step for European battery supply chain security
Vulcan Energy Resources Limited (Vulcan, ASX: VUL, FSE: VUL, the Company) is pleased to announce the Start of Production (SOP) of the first Lithium Chloride (LiCl) product at Vulcan’s Lithium Extraction Optimisation Plant (LEOP) in Landau, Germany.
Highlights
- First LiCl produced from LEOP, heralding the first lithium chemicals domestically produced from a local source in Europe, for Europe.
- LEOP is showing strong early results with consistently over 90% (up to 95%) lithium extraction efficiency from its Adsorption-type Direct Lithium Extraction (A-DLE) unit, replicating what Vulcan has seen in its lab and pilot plant operations, and in line with its commercial plant expectations and Vulcan’s financing model.
- The SOP follows over three years and more than 10,000 hours of successful in-house A-DLE piloting by Vulcan, showing high lithium recoveries and thousands of cycles of adsorbent life with no material degradation.
- Representing a more than €40m investment by Vulcan, LEOP is an optimisation, operational training and product qualification testing facility, to enable operational readiness for when the Phase One commercial facility is completed.
- Once Phase One commercial production commences, it is estimated that Vulcan’s integrated renewable energy and ZERO CARBON LITHIUM™ business will produce enough lithium for approximately 500,000 EVs.
- Vulcan has proven that the sustainable lithium production process known as A-DLE, which accounts for 10% of global lithium production today, can be successfully applied in the Upper Rhine Valley Brine Field.
- The Upper Rhine Valley Brine Field in Europe contains Europe’s largest lithium resource and is also a source of geothermal renewable heat. This will allow Vulcan to produce its lithium using geothermal renewable energy, decarbonising the carbon footprint of lithium production for Battery Electric Vehicles.
MD and CEO Cris Moreno stated, “This significant milestone marks a pivotal moment in Vulcan’s journey towards revolutionising domestic lithium raw material supply for Europe’s Battery industry. Vulcan’s LEOP facility is equipped with world-leading technology designed to showcase the efficiency of our A-DLE process and environmental benefits, whilst training our commercial production team in a pre-commercial environment as we build the Phase One commercial plant. It is encouraging to see LEOP deliver extraction efficiency in line with our expectations. I would like to thank our determined project execution and operations team for getting us to this landmark. We look forward to providing further updates on our Central Lithium Electrolysis Optimisation Plant (CLEOP) as we aim to produce Europe’s first fully integrated lithium battery chemicals from our own domestic resource, and also to providing updates on Phase One of the Zero Carbon Lithium™ Project, including financing, in the coming months.”
Next steps
The LiCl produced by LEOP represents the first lithium chemicals fully produced from a locally sourced raw material, i.e. extracted and then processed locally, at this plant scale in Europe. During hot commissioning and startup of LEOP, a generic aluminate-based lithium adsorbent was used, that has been used before in Vulcan’s lab and pilot plants. Vulcan’s internally developed high-performance aluminate-based lithium adsorbent, VULSORB®, will be used for the long-term operation. The next step will be conversion to a battery-grade lithium chemical in Vulcan’s downstream optimisation plant. The LiCl product (40% weight solution) produced from LEOP will be transported to Höchst Industrial Park Frankfurt, where Vulcan is currently completing its CLEOP which will convert the LiCl into battery grade Lithium Hydroxide Monohydrate (LHM). Once CLEOP is in operation, which is expected in mid-2024, Vulcan will have produced the first fully integrated lithium battery chemicals in Europe, including conversion to a battery-grade chemical, with the co-production of renewable energy and heat. These optimisation plants are comparable to Vulcan’s Phase One, commercial plants, with similar process flowsheets, with the commercial project aiming for 24,000 tonnes per annum of lithium hydroxide production capacity, the financing process of which is currently being led by BNP Paribas.
Media inquiries:
Annabel Roedhammer
Vice President Communications
aroedhammer@v-er.eu
+49 (0) 1511 410 1585